Car Exterior Components Plastic Welding: What You Need to Know
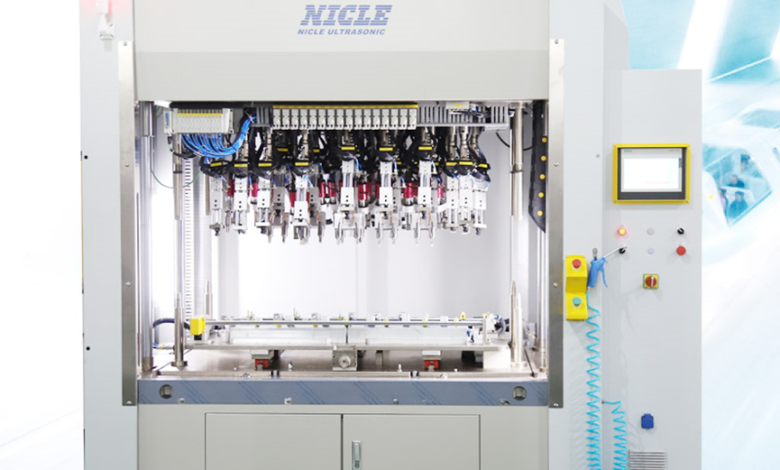
In modern automotive manufacturing, plastic welding has become a crucial method for joining plastic components, particularly in the assembly of car exterior parts. The ability to weld plastic components accurately, efficiently, and securely is a key to maintaining both the structural integrity and the aesthetic quality of a vehicle.
In this article, we’ll explore the key techniques, tools, and materials used in car exterior components plastic welding, including cutting-edge technologies like auto exterior parts ultrasonic welding.
We’ll also discuss the importance of selecting the right equipment, such as an auto exterior parts ultrasonic welding machine, and finding a reliable automotive exterior parts ultrasonic welding supplier or auto exterior parts ultrasonic welding manufacturer.
Why Plastic Welding is Important for Car Exterior Components
Car exterior components include bumpers, side panels, door trim, and light housings, which need to be durable, lightweight, and resistant to environmental factors like UV radiation, extreme temperatures, and physical impact.
The ability to fuse plastic components together creates strong, seamless bonds, ensuring the parts remain intact and function as intended over the lifespan of the vehicle. Car exterior components undergo a great deal of stress, from daily wear and tear to collisions and environmental exposure.
Plastic welding is therefore critical for creating bonds that are strong, durable, and capable of withstanding these challenges. As plastic materials evolve to offer even better performance, advanced welding techniques are essential to keep up with the demand for higher-quality, more resilient automotive parts.
Key Techniques in Car Exterior Components Plastic Welding
There are several key techniques used in car exterior components plastic welding, each of which offers specific advantages depending on the materials being used, the design of the parts, and the production requirements.
The two most common welding methods for automotive exterior components are ultrasonic welding and heat staking, both of which deliver reliable results when performed properly.
1. Ultrasonic Welding for Car Exterior Components
Ultrasonic welding is one of the most advanced techniques used in car exterior components plastic welding. This method uses high-frequency ultrasonic waves to generate heat through friction, which causes the plastic parts to melt and bond together.
Car exterior components plastic welding is used for a wide range of car exterior components, such as headlights, grilles, and fender flares, ensuring a strong, uniform bond that enhances the overall quality of the part.
For those interested in a multi-head solution, a reliable car exterior components plastic welding supplier can provide advanced machinery to accommodate larger production runs.
2. Heat Staking
Heat staking involves applying heat and pressure to a plastic component until it softens, at which point the material is deformed to form a bond. This method is often used for components that require joining plastic parts with metal inserts or other materials.
Heat staking provides excellent strength and is commonly used in assembling parts like radiator tanks, air intake systems, and mounting points for various components.
While heat staking is not as common in car exterior components as ultrasonic welding, it still plays an important role in the automotive manufacturing process, particularly when metal and plastic components need to be fused together.
Tools and Equipment for Car Exterior Components Plastic Welding
The right tools and equipment are essential for ensuring precise, durable welds in car exterior components. Different welding techniques require specific machines and accessories, and selecting the correct equipment can impact both the speed and quality of production.
Below are some key tools and equipment used in car exterior components plastic welding.
1. Ultrasonic Welding Machines
An auto exterior parts ultrasonic welding machine is at the core of ultrasonic welding technology. These machines use high-frequency sound waves to create the heat and pressure needed to fuse plastic components.
The key components of an ultrasonic welding machine include the ultrasonic generator, converter, booster, and sonotrode. Each part plays a role in converting electrical energy into mechanical vibration and then directing this vibration to the workpiece.
When looking for an ultrasonic welding machine, it’s important to choose a machine that can accommodate the size and complexity of the car exterior parts being welded. Auto exterior parts ultrasonic welding machines come in various sizes, from smaller bench-top units for delicate components to larger, more powerful machines designed for high-volume production of large parts.
For instance, advanced ultrasound welders are available to meet specific production needs, offering robust, precise, and efficient welding capabilities for a variety of automotive exterior components.
2. Automated Welding Systems
Automated welding systems, such as robotic arms and fully integrated welding stations, have become increasingly popular in automotive manufacturing. These systems can be equipped with ultrasonic welding tools to perform precise, repeatable welding tasks at high speeds.
The integration of robotics ensures that car exterior components are welded with high consistency and minimal human intervention, reducing production costs and improving overall efficiency.
If you’re looking for a comprehensive solution, an automotive exterior parts ultrasonic welding supplier can help you find the right automated welding system to suit your needs. Robotic systems can also be programmed to perform other tasks such as assembly, inspection, and quality control, further streamlining the production process.
3. Welding Fixtures and Tools
Welding fixtures and tools are crucial for ensuring the accurate alignment and placement of plastic components during the welding process. These fixtures are designed to hold parts securely in place while the welding machine does its work. They help ensure that each weld is made precisely in the right location, reducing the risk of defects or inconsistencies.
When setting up a welding station, it’s essential to ensure that the fixtures are designed specifically for the types of car exterior parts being welded. This ensures optimal results and reduces the risk of misalignment or damage during welding.
Materials Used in Car Exterior Components Plastic Welding
Car exterior components are made from various types of plastic materials, each with its unique properties and welding characteristics. Some of the most commonly used plastics in automotive manufacturing include:
- Polypropylene (PP): This thermoplastic is lightweight, resistant to chemicals, and has excellent impact resistance. It is commonly used for bumpers, side panels, and other exterior components.
- Polycarbonate (PC): Known for its high strength and optical clarity, polycarbonate is often used for headlights, taillights, and other transparent exterior parts.
- Acrylonitrile Butadiene Styrene (ABS): ABS is used for components requiring impact resistance and toughness, making it a popular choice for automotive exterior parts like grilles and trim.
- Polyamide (PA): Also known as nylon, polyamide offers high strength and resistance to wear and tear, making it suitable for components like fender liners and underbody parts.
Each of these materials requires specific welding techniques to achieve the best results. Car exterior components plastic welding specialists must ensure that the chosen welding method is compatible with the type of plastic used for each part to achieve the desired strength and performance.
Finding the Right Automotive Exterior Parts Ultrasonic Welding Supplier
When looking for an automotive exterior parts ultrasonic welding supplier or auto exterior parts ultrasonic welding manufacturer, it’s important to select a partner with experience in the automotive industry.
A reliable supplier should offer high-quality ultrasonic welding machines, as well as support for installation, training, and maintenance. Choosing the right supplier can ensure that your production line runs smoothly and efficiently, while also reducing the risk of defects and downtime.
Additionally, it’s important to select a supplier who can provide technical support and help with troubleshooting. An experienced auto exterior parts ultrasonic welding manufacturer will have a deep understanding of the challenges involved in welding automotive components and can provide tailored solutions to meet your specific needs.
Conclusion
In the world of automotive manufacturing, car exterior components plastic welding is an essential process for producing high-quality, durable parts. Whether using auto exterior parts ultrasonic welding for precision bonding or heat staking for metal-plastic combinations, understanding the techniques, tools, and materials involved is key to achieving successful results.
By choosing the right equipment and working with experienced automotive exterior parts ultrasonic welding suppliers and auto exterior parts ultrasonic welding manufacturers, manufacturers can ensure the production of strong, reliable car exterior components that meet the highest industry standards.
As technology continues to evolve, the future of car exterior components plastic welding looks even more promising, with innovations in automation, materials, and techniques offering exciting new possibilities for the automotive industry.